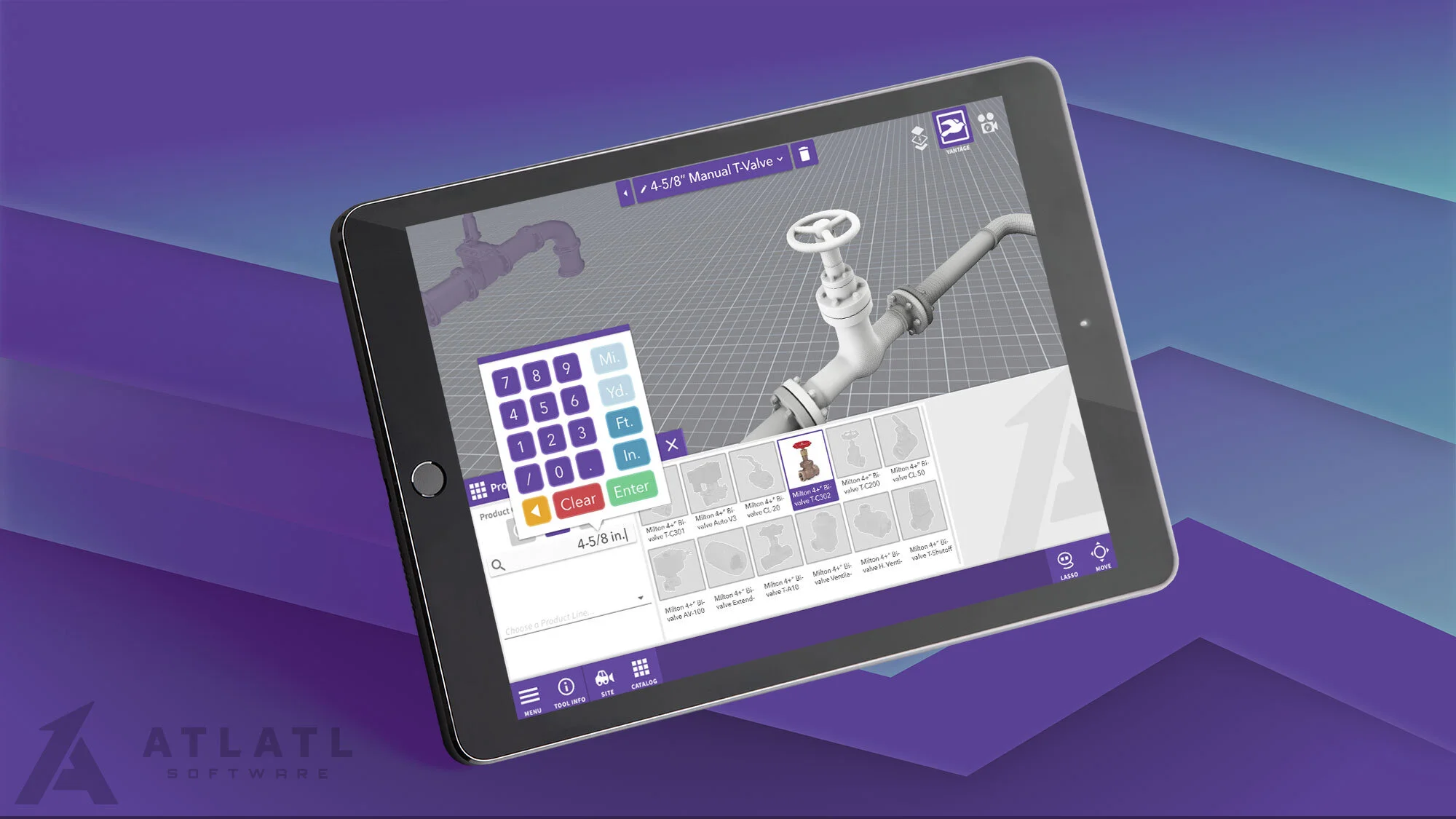
Atlatl Visual 3D
Bringing functional AR to manufacturing sales
Atlatl Software needed to distill a costly stable of single-client apps into a single, full-featured 3D visualization platform to satisfy a broad range of manufacturing clients and guide them into the digital age.
By conducting deep industry research and harnessing the combined knowledge of disparate end-users, I envisioned and designed a unified Atlatl platform, leading teams of designers and developers to deliver revolutionary predictive systems and controls for touch interfaces.
Roles:
Lead Product Design
Lead UX Design

Highlights:
10M+
Revenue
Generated
23
Features
Designed
5
Client Training Workshops
750+
Design Doc
Pages Written
Challenges:
Beta Within a Year
With funding rounds, contracts, and patents on the line, time to launch was critical. My team delivered early and had added systems that extended functionality beyond our initial goals.
Usability Concerns
Many of our target users were long time manufacturing salespeople, used to sketching out quick diagrams on paper. I had to convince them to adopt our solution while keeping it accessible.
Deep Versatility
From cryogenic piping to conveyor belts to backhoes, Atlatl’s customers were operating vastly different businesses, and the platform had to be designed to deliver immediate value to them all.
Intense Complexity
Each business had its own set of sales and assembly rules, and each industry had its own guidelines and standards. All of this had to be calculated automatically, and the UI had to simplify them for the user.
Selected Features:
3D Camera Controls
Designing intuitive 3D camera controls for a decidedly pencil-and-paper workforce seemed like a challenge even without the requirement that the controls be touch-based.
Atlatl’s “vCPQ” 3-D configurator had been developed around the concept of quoting Configured to Order Products, such as switching out one type of tool for another on the arm of a construction machine. I was brought on to create systems for Engineered to Order Products, which demanded a much more advanced suite of controls for navigating 3-D space.
The solution needed to work on an iPad as well as in WebGL, and each had to have different but related control schemes. The core camera improvements I devised and managed were the vantage controls (allowing users to swipe the camera to pre-determined or custom locations), the orthographic projection toggle, the elevation layers control, and the orbital and focus controls.
Waypoint Network
A fully implemented, touch-controlled 3D node network that tracks connection order, product dimensions, flow directionality, arbitrary angles, and snaps nodes to allowable positions based on a variable system of business rules and simulated physics.
In order to facilitate the new levels of complexity possible for client customization in Atlatl’s 3-D Configurator, we needed a system for product layout that would be easy enough for a salesperson to use while still providing enough detailed data and complexity for the client’s engineers and our real-time engineering rules to populate a BOM/quote with accurate parts and components.
For a year I led a small team to produce a fully-featured, platform-defining system from initial sketches to 100+ page design document, to user training, acceptance testing, and launch.
The Waypoint System became the foundation of the product roadmap, and led to redefining the way that nearly everything else in the application functioned, from movement and dimensioning to client workflows and solutions.